Axis was equipped with Multi Jet Fusion HP technology in July 2017. Since then, we’ve been doing all we can to promote this technology for small and medium production runs.

The Multi Jet Fusion HP is a machine for producing parts by powder sintering. At Axis, we only use PA 12.
This 3D printing technique involves several stages.
– The first step consists of depositing a layer of powder by means of a carriage in the manufacturing chamber.
– A second pass is then made by another cart, which deposits fusing and contouring agents. On his return journey, he is responsible for dropping off the various agents. The fusion lamps allow you to sinter the different materials. The parts will therefore be manufactured in succession. Ventilation then cools the whole, hardening the material layer by layer as it passes through.
– Once the parts have been produced, it is important to allow them to cool. If the parts leave the machine too early, there is a high risk of heat distortion of the sintered parts. Finally, the cooled parts are removed from their cooling station and dewaxed.
HP Multi Jet Fusion enables you to produce large numbers of parts more quickly. Thanks to its speed and mechanical precision, we prefer this technology for small/medium production runs.
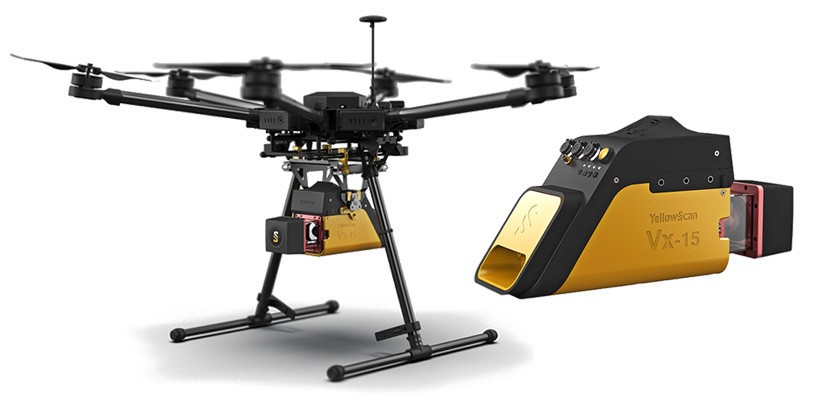
For example, we have been working with Yellowscan for several years. This company specializes in the production of topographic devices that produce 3D centimetric terrain models. These devices are installed on drones which, in just a few minutes, can produce a variety of maps. These tools are used for a variety of purposes, including archaeology, civil engineering and mining.
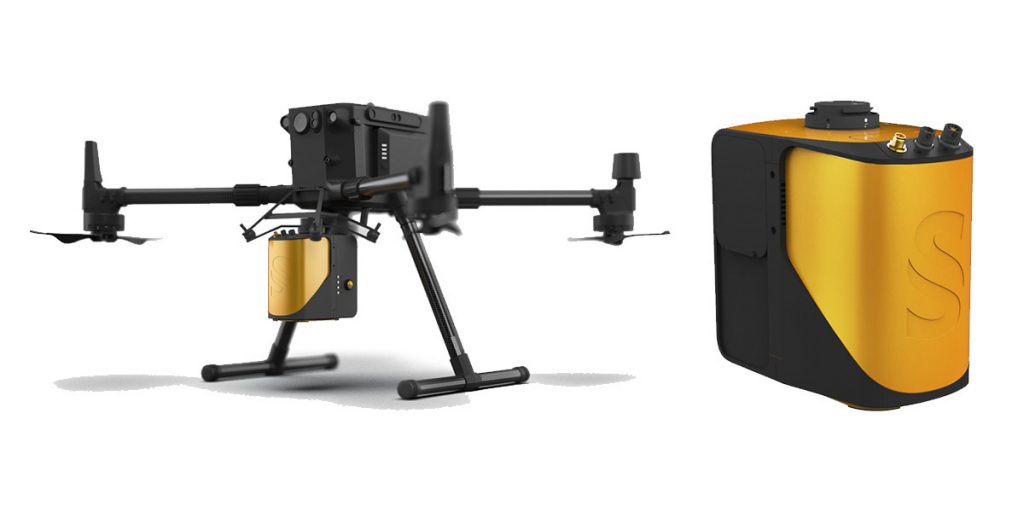
As part of this collaboration, we produce parts in HP Multi Jet Fusion with different types of finish. The aim with this material is to produce technical and resistant parts in a relatively short time. It’s also a 3D printing technique that can be launched into production, enabling small and medium production runs to be achieved in less time than with vacuum casting.
In the case of sintered parts, the initial porous appearance must be smoothed with a primer applied in one or more coats. Our modelers can then apply a paint finish according to our customer’s specifications. Our teams can counter-type samples supplied by the customer or carry out color research to obtain a unique color. We can also apply other types of finish, such as black coloring, which transforms the initial charcoal-gray color of the parts, or add a graining finish to the parts.
If you are interested in this 3D printing technique, please do not hesitate to contact us via the contact form or directly via our consultation e-mail address axis@axishello.com