Axis has been producing prototypes using several 3D printing techniques since its inception. Vacuum casting is one of them, and a major part of our company’s know-how.
The vacuum casting technique is often favored to avoid or initiate more costly production using metal injection molds. Vacuum casting first uses stereolithography to create a master model around which we produce a silicone mold for casting parts in polyurethane vacuum machines. Thanks to this3D printing technique, we were able to create the Louboutin display in the brand’s iconic color, the red of the designer’s soles.
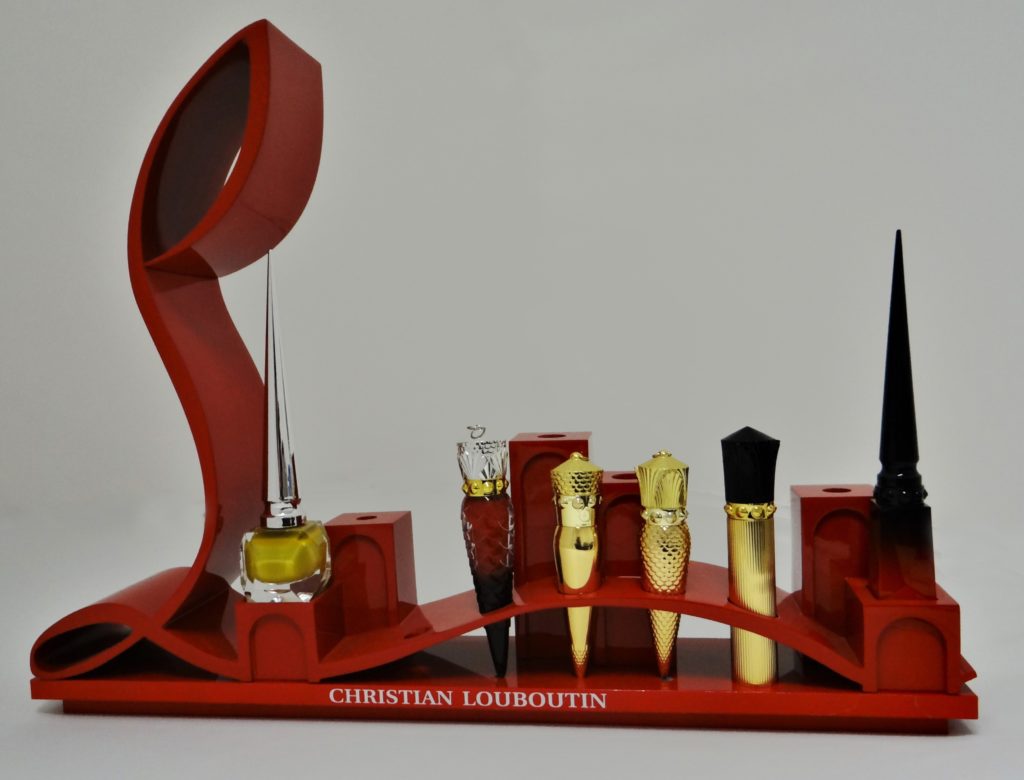
Christian Louboutin first ventured into the world of cosmetics with the creation of a red varnish with a spiked cap reminiscent of the heel of the designer’s shoes. The actual beauty part of the brand has been developed since March 2018 in collaboration with Puig (a Spanish brand specializing in the creation of perfumes and cosmetics).
Being a mini-series, we were able to produce this display for the release of Rouge Iconique, even though we specialize in rapid prototyping.
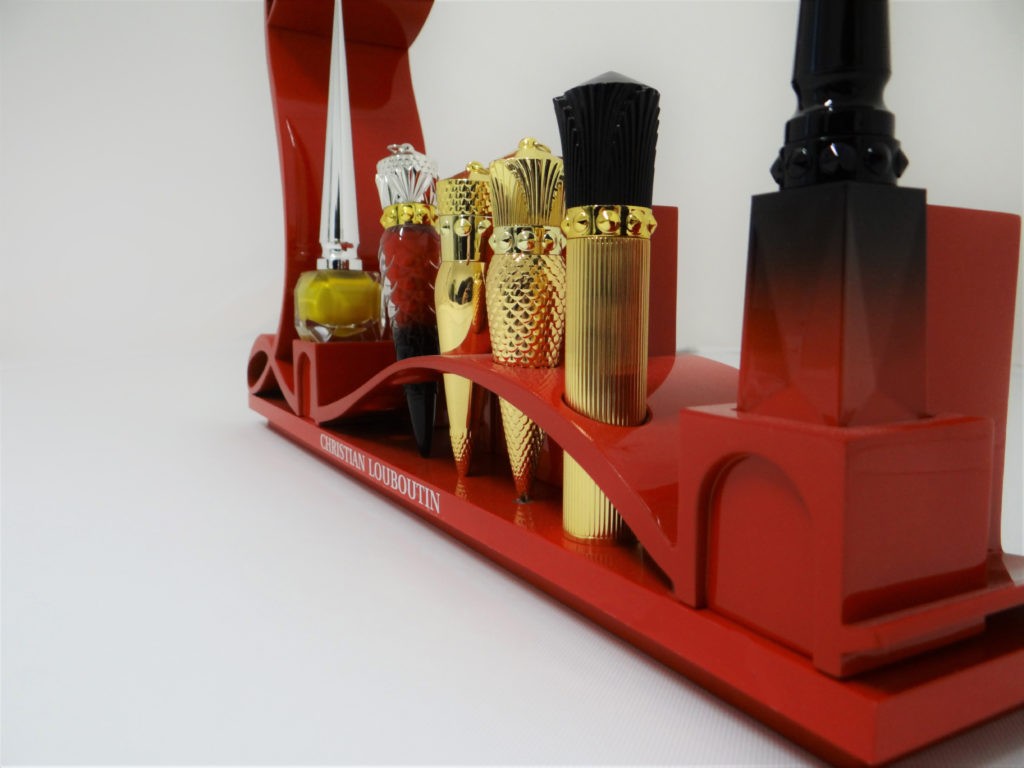
To achieve this high-gloss red finish, it’s first important to apply a high-gloss finish to the master model created in stereolithography. It’s during the mixing of polyurethane materials (known as PU) that we add a color to tint the parts in the mass. Note that the silicone mold used for vacuum casting has a limited lifespan, ranging from 10 parts (for the most corrosive PU materials) to a maximum of 30 parts for elastomer parts.
This type of highly detailed part is particularly time-consuming to produce in vacuum casting, as great care must be taken when removing the castings from the silicone mold to obtain the part. With this additive manufacturing process, we produce parts one by one, unlike processes such as stereolithography or powder sintering, so we can launch several parts simultaneously. Vacuum casting is therefore a technique that can be used to produce parts with materials close to those of injection molding, with a finish and appearance close to those of mass-produced parts, but taking longer to produce.

Vacuum mini-series casting is therefore at the heart of our business, because it’s an important stage in projects that need to be tested before being launched in injection molding, and therefore in larger production runs. We have a wide range of materials, from silicone to soft materials and injection molding materials such as ABS. Also, some prototypes need to have special technical properties such as fire resistance (ULV0) or food compatibility (Food safe), which is possible with vacuum casting.
If you have any mini-series production requirements, either before or in place of injection molding, please don’t hesitate to contact us!